Here in this term paper description is given about a type of polyamide fibre i.e.
Nylon-66. Here in this paper the methods of preparation of monomers, polymerisation, manufacturing methods of nylon-66, spinning process to obtain fibres, different properties and wide range of applications and uses of nylon-66 are discussed. In this paper data are represented in the form of flow charts, histogram and pie charts for easy understandings. This paper covers all the processes related to nylon-66.
1. Introduction There are several polyamides, which have been developed as fibres. The generic word for these products is 'Nylon'. Nylon is defined as a generic term for any long chain synthetic polymeric amide which has recurring amide groups as an integral part of the main polymer chain and which is capable of being formed into a filament in which the structural elements are oriented in the direction of the axis.
DuPont researchers led by Dr. Wallace Carothers, invented nylon-66 polymer in the 1930s. Nylon, the generic name for a group of synthetic fibers, was the first of the “miracle” yarns made entirely from chemical ingredients through the process of polymerization. Nylon 66 polymer chip can be extruded through spinnerets into fiber filaments or molded and formed into a variety of finished engineered structures.Nylon-66 fibre is a member of the large group of polycondensation products of dicarboxylic acids and diamines with fibre forming properties. The individual member refers to the number of carbon atoms respectively in the diamine and dicarboxylic acid chains.
Nylon-66 (polyhexamethylene diamine adipamide) is a polyamide made from adipic acid and hexamethylenediamine by polycondensation. The resulting polymer is extruded into a wide range of fiber types. The fibers are drawn, or stretched, in a process that increases their length and reorients the material’s molecules parallel to one another to produce a strong, elastic filament. The thermo-plasticity of nylon permits permanent crimping or texturing of the fibers and provides bulk and stretch properties.
The nylon developed by Carothers at Du Pont was nylon 66. Because of the importance of starting out with equal amounts of the two reactants, salts of the diamine and of the diacid are made and then used in the commercial synthesis of nylon 66.
2. HISTORY The development of nylon was started from 1927 by means of many researchers, notably among them W.H.Carothers and P.Schlack. The research activities preceding the manufacture of nylon yarn can be divided into the following categories:
(a) Fundamental research activities which provided the foundation for the development.
(b) Different types of polyamides, their synthesis, manufacture and their suitability for use as a new fibre. This includes all types of polyamides like aliphatic, aliphatic-aromatic and fully aromatic polyamides.
(c) Commercial production of the fibres.
(d) Development of the properties and serviceability of the fibres.
Polyamides are characterized according to the number of carbon atoms present in the structural unit of the molecule. These are:
(a) Nylon made from condensation of a diamine and a dicarboxylic acid is classified according to the number of carbon atoms present in the amine and acid respectively. Thus nylon formed by hexamethylene diamine (NH2 (CH2)6-NH2) having 6 carbon atoms and sebacic acid (COOH-(CH2)8-COOH) having 10 carbon atoms is generally referred to as nylon 6,10
(b) Nylon, made from amino acid, is classified according to the number of carbon atoms present in the acid. It will have only one number. For example, Nylon 6 can be made from amino acid having 6 carbon atoms i.e., amino caproic acid or its condense product caprolactum.
So the numbers indicate the number of carbon atoms in the monomer taking part in the polymerisation. In general,
Table 12.1 Raw materials of different Nylons Nylon | Raw materials |
Nylon 4,6 Nylon 6,6 Nylon 6, 1 0 Nylon 6,12 Nylon 3 Nylon 4 Nylon 6 Nylon 7 Nylon 11 Nylon 12
| 1 ,4 diamino butane, Adipic acid Hexamethylene diamine, Adipic acid Hexamethylene diamine, Sebacic acidHexamethylenediamine, Dodecanedioic acid Acrylamide 2-pyrolidane Caprolactum Lactum of heptonoic acid W-amino-cendecanoic acid Dodelactum
|
3. The Nylon Fiber Design Advantage In 1939, the introduction of nylon into sheer stockings revolutionized the women’s hosiery market. Silk and cotton were quickly replaced by this more durable and easy-care product. Nylon soon found its way into other end uses. In parachutes and fishing line, nylon provided a moisture- and mildew-resistant replacement for silk. In flak vests, nylon offered a strength and durability previously unattainable for protection against shell fragments. And, when used as aircraft tire reinforcement, nylon enabled heavy bombers to land safely on improvised air strips. Today, as the global leader in nylon polymer, DuPont offers a wide range of nylon-66 polymer types for use in industrial, textile, and furnishing/floor covering applications.
4. Advantages of Nylon-66 Nylon 66 is superior in many applications to nylon 6—the other large volume nylon—due to its outstanding dimensional stability, higher melting point, and more compact molecular structure (see Figure 1). Nylon 66 exhibits only about half the shrinkage of nylon 6 in steam, for instance. And, with a less open structure, the 66 fiber has good dye wash fastness and UV light-fastness, and excellent performance in high-speed spinning processes. Typical advantages of nylon 66 over nylon 6 are its
- Higher tensile strength in use,
- Excellent abrasion resistance, and
- Higher melting point.
Nylon 66 provides high tensile strength for
- Tough fibers at fine deniers,
- Excellent performance for tyre applications, and
- High-speed mill processing.
Excellent abrasion resistance makes nylon-66 polymer ideal for use in
- Carpets,
- Upholstery, and
- Conveyor belts.
The rubber industry takes advantage of the higher melting point of nylon 66 in high-temperature tire curing. A high melting point also results in a fiber with
- High stretch and recovery in false-twist textured Yarns (e.g., hosiery and socks) and
- Thermal stability in high-temperature coating operations.
5. Use of Nylon-66 in Fiber Manufacturing The processing of nylon usually begins by conditioning the received chip, with or without an increase in the asreceived molecular weight. The chip is then melted, usually in a screw-type extruder, and spun into filament form. The filamentsare then packaged in a process that may include drawing, bulking, or cutting into lengths of staple.
6. Preparing Nylon-66 Chip Chip is normally conditioned in an inert atmosphere at temperatures in the 120–180°C (248–356°F) range. Processors may employ higher temperatures to increase molecular weight, especially for industrial uses. Both batch- and continuous-type conditioners may be used. It is important to avoid excessive exposure of the chip to oxygen, which may lead to degradation and yellowing of the product.
7. Remelting Nylon 66 Chip Remelting is normally performed in a single or twin screw-type extruder, although the melting can be done in a heated grid-type melter. Single screws are preferred for smaller spinning plants because of their simplicity. Twin screws are preferred for larger installations or when more extensive mixing during remelt is required. Equipment must have the capability of heating the polymer to 280–290°C (536–554°F). Handling of the Molten Polymer Nylon 66 may produce undesirable cross-linked material (gel) if processing temperatures and holdup times are not properly maintained. Care must be taken to eliminate areas of stagnation in the screw and in the polymer piping. Good engineering practices require the application of optimum shear rates and frequent mixing of the melt. Conversion—Molten Polymer to Final Product Form Due to the wide variety of nylon 66 products that can be produced and the range of processing equipment available, it is beyond the scope of this bulletin to specify ideal processing conditions. In general, most modern filament-producing equipment will process nylon 66 polymer adequately.
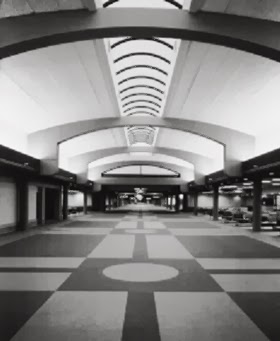 |
|
8. PREPARATION of the Monomer Adipic Acid (ADA) and Hexamethylene diamine (HMD) are used as raw materials for Nylon-66 Polymer. The schemes of preparation of adipic acid and hexamethylene diamine are shown in Figure.
8.1. ADIPIC ACID MANUFACTURE 8.1.1 FROM CYCLOHEXANOL Mostly cyclohexane (CH), cyclohexanol (CHL) and cyclohexanone (CNH) are used to obtain adipic acid (ADA). For oxidation, only nitric acid and oxygen can be used economically. The most important process is the oxidation of cyclohexanol with 50% nitric acid at 60-70°C. In a stainless steel kettle the cyclohexanol is added to the acid under cooling and stirring, the acid is crystallized from water. The yield exceeds 85%.
8.1.2. From Cyclohexanone The oxidation of cyclohexanone with nitric acid requires higher temperatures. Also cyclohexanone is oxidized in the presence of acetic acid as diluent and with 0.1% manganese acetate or nitrate at 80-1.00°C. The yield is about 70%.
8.1.3 From Cyclohexane The simplest method for the production of adipic acid is direct oxidation of cyclohexane. Most useful is the catalytic oxidation with air by soluble Mn or Co catalysts at 120-150°C. The reaction is interrupted at a conversion of 10-15% and leads away to a mixture of cyclohexanol and cyclohexanone in equal amounts with adipic acid, cyclohexanol adipate, and lower aliphatic acids. The unchanged product is recycled and the crude oxidation product fractionated. Since cyclohexane is an important petrochemical product, production of cyclohexanol and cyclohexanone is based on this process.
8.2. ADIPONITRILE Manufacture Adiponitrile is the intermediate for the production of hexamethylene diamine. It can be produced by different methods:
8.2.1. VAPOUR PHASE FROM ADIPIC ACID AND AMMONIA
This method involves condensation from ammonia and adipic acid in the vapor phase. Adipic acid is vaporized with an excess of ammonia gas (mol. ratio 20:1) at 350°C over a catalyst of boron phosphate. The reaction is endothermic at 57 cal/mole. The yield is 88%.
8.2.2. Liquid Phase Process In a liquid phase process, ammonia is introduced in molten adipic acid at 200-250 in the presence of such alkyl or alkyl phosphates catalysts like 0.1 -0.5% phosphonic acid or boron phosphate. The yield is around 88%.
8.3. 1, 4 DlCHLOROBUTANE AND SODIUM CYANIDE 1, 4 Dichlorobutane can be obtained by addition of chlorine to butadiene. This can be converted to 1, 4 dicyanobutane by NaCN. Dry NaCN is mixed with adiponitrile as diluent and the calculated amount of 1, 4 dichlorobutane is added at 185-190°C. By addition of water, the oily layer is distilled. The yield is about 95%.
8.4. ELECTROHYDRO DIMERISATION OF ACRYLONITRILE
By electrohydro dimerisation, yield will be 82%. The pH will be 9 and the current density will be 2 to 30 MA/dm2. The cathode potential was found to be independent of pH above 2.5. The overall reaction will be
2 CH2 CHCN + 2 H+ + 2e- → NC (CH2)4CN
8.5. Hexamethylene Diamine - Manufacture HMD is manufactured exclusively by the hydrogenation of the dinitriles. Palladium is used as catalyst. Another effective catalyst is cobalt oxide mixed with calcium oxide. In all cases, the reaction must be carried out in the presence of excess ammonia. Pure HMD is a colourless crystal, melting at 40°C, B.P. 100°C, soluble in water, and alcohol.
9. POLYMERISATION Nylon-66 production from adipic acid and hexamethylene diamine comprises four steps: (1) Salt preparation (2) Polycondensation (3) Melting. (4) Extrusion. A schematic diagram of Nylon 66 polymer formation process is shown in Figure.
10. Nylon 66 Salt (NH salt) High molecular weight nylon 66 is only obtained if equimolecular amounts of the components are used. An excess of the components would terminate the chain by formation of an acid or amino end group. So stoichiometric portions of hexamethylene diamine and adipic acid must be used (amine to acid of 1:1). For this reason, the salt of 1 mole adipic acid and hexamethylene diamine (AH salt) is used as intermediate. The hexamethylene diamine is used as a 60-70% solution and the adipic acid as a 20% solution. The monomers are fed and mixed in the mixer and transferred to the prepolymeriser. Methanol is added and the reaction takes place. Methanol can be refluxed. The separated salt is centrifuged and washed with methanol. It is stored as a 60% solution in distilled water. It is a snow white crystal (mp - 190°C). Owing to all these constraints, batch processing is used.
11. POLYCONDENSATION The concentrated salt solution is then fed to the polymerisation reactor, where the second-stage of the reaction begins (Fig 12.5 c). 60% Aq. Solution of the salt in distilled water, 0.5% acetic acid (stabilizer) is pumped into an autoclave. Increased temperature and pressure are used to initiate the polymerisation reaction. So the autoclave is heated to 275°C. The pressure is generally kept constant (1.8 MPa). Before the reaction, the autoclave is purged with very pure nitrogen (less than 0.005% oxygen) to avoid degradation and discoloration of the polymer. When the temperature of the batch reaches 275°C, the pressure is allowed to fall to atmospheric pressure. The batch is held at 270°C and atmospheric pressure for half an hour to allow removal of the water vapor. The heating is continued until all water has been distilled off. Towards the end of the distillation, the autoclave is evacuated. The polymer is obtained as a clear, low-viscous melt which is removed from the autoclave by pressure with pure nitrogen. The melt is extruded through the bottom of the reactor to form a ribbon. It is solidified and cooled in cold water cut into chips and dried. The dried chips are stored in a storage hopper in a similar manner like that of Nylon 6.
12. SPINNING Nylon has sufficient stability of the melt and adequate viscosity. So it can be spun in the molten state with usual velocity (upto 2000 m/min). The polymer chips are fed to the hopper and then it is melted and homogenized in an extruder. The molten polymer after filtration is passed to the spinnerets. The melt is pumped through this system and solidifies immediately on contact with air. Cross air flow is used for solidification. The melting temperature for spinning is around 300°C. After spinning like nylon 6, the flows are stretched to get the desired elongation. Details of spinning and stretching processes are discussed in Chapter - 2 (Fig 2.1 and 2.6). The different parameters which can be varied to influence fibre properties are: (a) Mass output, (b) Winding speed, (c) Spin draw ratio, (d) Draw ratio and (e) Draw temperature. The properties which will be considered are: tensile strength, elongation, modulus, crystallinity and orientation.
13. PROPERTIES 13.1. PHYSICAL PROPERTIES Like Nylon 6, different types of Nylon 66 fibre exhibit different physical properties.
Physical Properties | Staple Fibre | Normal Filament | High Tenacity Filament |
Density (gm/cc) | 1.13 | 1.14 | 1.15 |
Moisture (%) at 65% rh 100% rh |
4.0-4.5 6.0-8.0
|
4.0-4.5 6.0-8.0
|
4.0-4.5 6.0-8.0
|
Tenacity (g/d) Dry Wet |
3.0-6.8 2.5-6.1 |
2.3-6.0 2.0-5.5 |
6.0-10.0 5.1-8.0 |
Elongation (%) | 16-75 | 25-65 | 15-28 |
Stiffness (g/d) | 10-45 | 5-24 | 21-58 |
13.2. Thermal Properties Because of different structure, the melting point will occur in the range of 249°C to 260°C. The glass transition temperature of this fibre is in the range of 29°C- 42°C. The softening temperature i.e., the sticking temperature is 230°C. The fibre discolors, when kept at 150°C for 5 hours. The heat deflection temperature is 70°C. The decomposition of this fibre starts at 350°C.
13.3. Chemical Properties Nylon 6, 6 fibres is more resistant to acids or alkalis in comparison with nylon 6 fibre because of light intermolecular forces present in the structure. The fibre is unaffected by most mineral acids, except hot mineral acids. The fibre dissolves with partial decomposition in concentrated solutions of hydrochloric acid, sulphuric acid and nitric acid. The fibre is soluble in formic acid. In a similar way, the fibre is attacked by strong alkalies under extreme conditions otherwise it is inert to alkalis. The fibre can be bleached by most of the bleaching agents. The fibre is mostly insoluble in all organic solvents except some phenolic compounds.
The fibre has excellent resistance to biological attacks. Prolonged exposure to sunlight causes fibre degradation and loss in strength.
The fibre can be dyed by almost all type of dyestuffs like direct, acid, metal-complex, chrome, reactive, disperse and pigments. However only acid and metal complex dyes are preferred because of higher fastness properties.
14. Types of Nylon-66 products Manufactured - Nylon 66/6
- Nylon 66/6, 10% Glass Fiber Reinforced
- Nylon 66/6, 20% Glass Fiber Reinforced
- Nylon 66/6, 30% Glass Fiber Reinforced
- Nylon 66/6, 40% Glass Fiber Reinforced
- Nylon 66/6, Mineral Reinforced
- Nylon 66/6, 60% Glass Fiber Reinforced
- Nylon 66/Nylon 6 Blend, Glass Fiber Filled
- Nylon 66, Unreinforced
- Nylon 66, Impact Grade
- Nylon 66, Unreinforced, Flame Retardant
- Nylon 66, Heat Stabilized
- Nylon 66, Extruded
- Nylon 66, Film
- Nylon 66, Nucleated
- Nylon 66, PTFE Filled
- Nylon 66, MoS2 Filled
- Nylon 66, Glass Bead Filled
- Nylon 66, 30% glass filled, extruded
- Nylon 66, Mineral Filled, NCG Fiber Filled
15. Advantages of DuPont Nylon 66 in Specific Fiber Applications
When processed into fiber form, nylon 66 polymer offers many advantages for customer applications.
Hosiery - Excellent high-speed processing
- High stretch and recovery
- High durability and strength
- Good hand
Weaving and Warp Knitting – minimizes yarn distortion possible during winding, warping, knitting, and weaving processes